Seit 2007 gibt es nun schon die EN-12142 „Ladungssicherung auf Straßenfahrzeugen – Aufbauten an Nutzfahrzeugen – Mindestanforderungen“ und die Fahrzeugaufbauten wurden mit den Jahren immer besser.
Es werden fast nur noch Aufbauten hergestellt, die dem Code XL-Profil entsprechen. Bezogen auf die Stirnwand bedeutet dies eine Mindestbelastbarkeit von 50% der technischen Nutzlast.
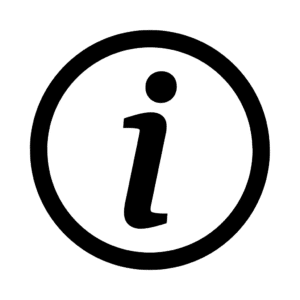
Der vermehrte Einsatz von Code XL-Aufbauten an sich ist eine gute Sache. In der Praxis werden jedoch immer wieder Fehler gemacht, weil den Beteiligten oft nicht bewusst ist, welche Randbedingungen zu beachten sind, damit die Festigkeiten des Aufbaus genutzt werden können, aber eine Überlastung verhindert wird.
Die Stirnwand
In der heutigen Ausgabe des LaSi-Blogs möchte ich die Stirnwand genauer beleuchten, sowie ein paar häufige Fehler und deren Abhilfe beschreiben.
Es haben sich bei den Stirnwänden zwei Bauweisen entwickelt. Die eine besteht aus einer vollflächigen Stahlstirnwand und die andere aus querliegenden Aluminium-Blanken. Beide sind mit den Eckpfosten verbunden.
Die Stirnwand ist das Bauteil eines Fahrzeugs, das im Fall der Fälle, nämlich der Vollbremsung mit einer Verzögerung von 0,8 g, die meisten Kräfte aufnehmen muss. Wer sich die Zeit nimmt, die EN-12142 in Ruhe zu lesen wird feststellen, dass es sich um eine Prüfnorm für Fahrzeugaufbauten handelt. Sie hat im ersten Schritt nichts mit der Ladungssicherung zu tun.
Erst ganz am Schluss wird in der Ausgabe 2016 gesagt, dass die nachgewiesenen Kräfte auch für die Ladungssicherung genutzt werden können. Mit dieser Aussage wird das, was die meisten sowieso schon gemacht haben, auf rechtlich sichere Beine gestellt.
Die Prüfnorm sagt, dass die Stirnwand auf der ganzen Breite geprüft werden muss. Die Mindestvorgaben für die Festigkeit (50% der technischen Nutzlast [P]) müssen in ¾ der Stirnwandhöhe erreicht werden.
Genau an der Stelle werden häufig Fehler gemacht, weil die Ladung nicht die ganze Breite der Stirnwand abdeckt oder keinen Formschluss zur Stirnwand hat. Was sind nun die Ursachen?
Das U-Profil an der Stirnwand
Einige Aufbauhersteller führen die Stirnwand so aus, dass sie ein flaches U-Profil bildet. Das linke Bild zeigt, dass die erste Paletten-Reihe zum Teil dahinter verschwindet.
Beim Beladen von der Seite muss der Verlader darauf achten, dass er die Paletten hinter das Profil schiebt, damit die Lücke geschlossen wird. Sofern der Gabelstapler über einen Seitenhub verfügt, ist das von Vorteil für den Ladevorgang, weil es das formschlüssige Stauen an der Stirnwand erleichtert.
Das Ergebnis könnte so aussehen, wie im Bild rechts. Beim Bremsen hat die Ladung die Stirnwand mitsamt der Halterung für die Anschlüsse verformt. Erkennbar an der Lücke zwischen der Halterung, die bleibend verformt ist, und der Stirnwand.
Die Lastverteilung
Eine weitere Fehlerquelle ist das Problem der Lastverteilung. Der Gesamtschwerpunkt der Ladung muss z.B. nach hinten verschoben werden, um die Antriebsachse nicht zu überlasten.
Im folgenden Beispiel sind die leeren Paletten nur symbolisch als Platzhalter zu sehen. In Echtzeit müssen sie natürlich gepackt sein.
Die Lösung des Problems besteht häufig darin, dass die Paletten einzeln hinter einander gestellt werden.
Dadurch wird die Kraft, welche die Ladung bei der Vollbremsung ausübt, auf eine zu kleine Fläche übertragen.
Die Stirnwand wird massiv überlastet und kann beschädigt werden.
Besser wäre die Lösung, indem zwei Paletten quer an der Stirnwand stehen, damit die ganze Breite genutzt wird.
Daran anschließend die Paletten einzeln, formschlüssig weiter stauen.
Wie viele einzeln gestaut werden müssen, hängt vom jeweiligen Ladungs- bzw. Palettengewicht ab.
Staupolster als Lückenfüller oder Abstandshalter
Eine weitere Lösung ist der Einsatz von Staupolstern als Lückenfüller oder Abstandshalter. Das ist jedoch eher ein Ansatz für sich regelmäßig wiederholende Situationen.
Dann allerdings ist es eine elegante, schnelle und effiziente Lösung. Sie sieht wie folgt aus:
Die erste Ladereihe steht direkt und formschlüssig an der Stirnwand, um die Kraft auf der ganzen Breite zu übertragen.
Dann wird ein entsprechend bemaßtes 3D-Staupolster eingebracht und die nächste Ladereihe formschlüssig und bündig dagegen gestaut.
Nach der zweiten Ladereihe kann nochmal ein Staupolster positioniert werden und danach der Rest der Ladung.
Wie sich der Gesamtschwerpunkt verändert, muss an Hand des Lastverteilungsplans überprüft werden.
Wichtig ist in jedem Fall, dass die Kraft gleichmäßig auf die Stirnwandbreite übertragen wird.
Einen Eindruck von falscher Stirnwand-Belastung zeigen die beiden folgenden Bilder:
Als Abstandshalter wurde ein A-Bock verwendet. Beim Bremsen hat die Ladung die Kraft über die zu kleine Fläche des A-Bocks auf die Stirnwand übertragen. Sie wurde dabei überlastet und gab nach. Die Aluminiumblanken wurden einfach durchgedrückt.
Die Ladung wurde so gestaut, dass sie die Stirnwand nicht auf der ganzen Breite abgedeckt hat.
Beim Bremsen wurde die Stahlstirnwand herausgedrückt. Die Verbindung der Stirnwand zu den Eckpfosten hat dieser Kraft nachgegeben.
Quelle: März 2016 – Transport Informations Service (tis-gdv.de)
Hier findet der interessierte Leser noch weitere Bilder und Details zu dieser Situation.
Fazit
Es ist also wichtig, dass sich die Verantwortlichen in einem Unternehmen, bei denen solche Situationen auftreten könnten, mit der Sache beschäftigen.
Typische Ladungen die solche Beschädigungen verursachen können sind z.B.: Gitterboxen, Octabins, Bigbags, IBC`s oder Vollpaletten mit Getränkekästen.
Ihr Sigurd Ehringer
<< Zum vorherigen Beitrag
Folge 35: Buchtlashing bzw. Slinglashing – Anwendung und Einsatzmöglichkeiten
Zum nächsten Beitrag >>
Folge 37: Lastverteilung am LKW – Wie berechnet man die Werte richtig?
Sigurd Ehringer
✔ VDI-zertifizierter Ausbilder für Ladungssicherung ✔ Fachbuch-Autor ✔ 8 Jahre Projektmanager ✔ 12 Jahre bei der Bundeswehr (Kompaniechef) ✔ 20 Jahre Vertriebserfahrung ✔ seit 1996 Berater/Ausbilder in der Logistik ✔ 44 Jahre Ausbilder/Trainer in verschiedenen Bereichen —> In einer Reihe von Fachbeiträgen aus der Praxis, zu Themen rund um den Container und LKW, erhalten Sie Profiwissen aus erster Hand. Wie sichert man Ladung korrekt und was sind die Grundlagen der Ladungssicherung? Erarbeitet und vorgestellt werden sie von Sigurd Ehringer, Inhaber von SE-LogCon.