Nachdem im vorangegangenen Blog die technischen Randbedingungen für Antirutschmatten auf der Basis der VDI-2700 Blatt 15 beschrieben wurden, geht es im folgenden Beitrag um deren praktische Anwendung.
Darüber lässt sich die Richtlinie nicht aus und es gibt auch wenig Bücherschreiber, die sich mit dieser Materie aus Sicht der Praktiker beschäftigen.
Antirutschmatten
Ich will versuchen, meine Erfahrung in griffige Beispiele zu packen. Grundsätzlich ist es nie verkehrt, in der Ladungssicherung mit Antirutschmatten (ARM) zu arbeiten. In den meisten Fällen bringen sie mehr Vorteile als Nachteile.
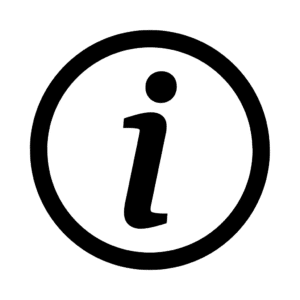
Häufig wird die Frage gestellt, wie dick sollen denn die Matten sein. Die weise Antwort lautet, es kommt darauf an. Rein rechnerisch und theoretisch physikalisch ist die Dicke der Matten unerheblich. Praktisch aber schon.
Die ARM müssen dafür sorgen, dass die zwei Oberflächen, nämlich die Ladefläche und die Ladungsteile/Ladungsträger, welche die Ladefläche berühren, über die Matten voneinander getrennt werden. Entkoppelt lautet der Fachausdruck dafür.
Nehmen wir zum Beispiel eine gleichmäßig gepackte Europalette mit 1.000 kg.
- Stehen z.B. 3 mm dicke Matten zur Verfügung, dann müssten alle drei Füße der Palette komplett mit ARM unterlegt werden. Das wären in etwa 0,414 qm.
- Wären 8 mm dicke Matten mit 150 x 200 mm zur Hand, würde eventuell 9 Pads genügen, eine Fläche von 0,27 qm.
- Eine elegante Lösung wären auch Streifen mit 200 x 1200 mm und 8 mm Dicke.
Die Kosten gehen immer nach Gewicht, auch wenn im Angebot ein Preis/Stück genannt wird. Aber der Preis ist nicht das ausschlaggebende, sondern die sichere Handhabung und das sichere Ergebnis.
Es gibt genügend Unfälle, bei denen der LKW-Fahrer die ARM nochmal korrigiert und der Staplerfahrer ihm die Palette auf die Finger setzt, weil er ihn nicht gesehen hat.
Verschiedene Möglichkeiten Antirutschmatten anzuordnen
Es gibt verschiedene Möglichkeiten, wie Antirutschmatten (ARM) gelegt werden können. Hier ein paar Beispiele:
Die aufwändigste Methode ist rechts zu sehen. Hier müssen 9 ARM-Pads exakt gelegt werden, um die Ladung von der Ladefläche zu entkoppeln.
Es ist vor allem dann notwendig, wenn die ARM sehr dünn (weniger als 4mm) sind.
Dieses Schema ist ebenfalls dann erforderlich, wenn die ARM dünn sind. Ein weiterer Nachteil liegt darin, dass sie sich nicht einfach korrigieren lassen.
Das Schieben geht meist nicht, weil sie nicht steif genug sind. Sie müssen also hochgehoben und neu positioniert werden.
Dieses Schema lässt sich anwenden, wenn die Matten mindestens 8 mm dick sind und die Palette gleichmäßig gepackt und belastet ist.
Dieses Schema ist ebenfalls möglich, wenn die ARM mindestens 8mm dick, 200 mm breit und 800 mm lang sind. Auch hier muss einigermaßen exakt positioniert werden.
Das ist die elegante Lösung, wenn die ARM mindestens 8 mm dick, 200 mm breit und 1200 mm lang sind. Der große Vorteil liegt darin, dass die ARM nicht exakt gelegt werden müssen, weil die Palette immer genügend Auflagefläche hat, damit sie von der Ladefläche entkoppelt ist.
Bei diesem Schema lässt sich auch die nächste Palette auf die überstehenden Streifen setzen. Korrekturen sind bei etwas Erfahrung nicht notwendig.
Anwendungstipps
Ziel muss immer sein, die Ladefläche und den Ladungsträger zu entkoppeln.
Das Bild rechts zeigt einen deutlichen Spalt zwischen Ladungsträger und Ladefläche.
Auch auf diesem Bild ist zu sehen, dass dickere ARM ein besseres Ergebnis bringen als dünne.
Die formstabile Kunststoffpalette ist mit zwei ARM-Streifen von der Ladefläche entkoppelt.
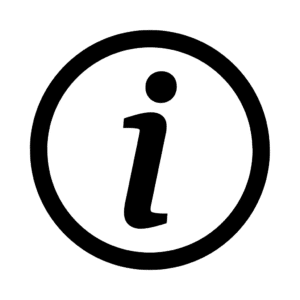
Das unzweckmäßige Verlegen der ARM führt häufig dazu, dass deren Wirkung stark herabgesetzt bzw. nicht vorhanden ist.
Die Beteiligten wähnen sich in einer Sicherheit, die tatsächlich nicht vorhanden ist.
Eine der häufigsten Ursachen ist die „nicht besenreine“ Ladefläche. Die ARM werden auf den mehr oder minder vorhandenen Schmutz, der sich auf der Ladefläche befindet, gelegt.
Dadurch ergibt sich eine Schicht zwischen ARM und Ladefläche, die teilweise die Verzahnung und damit den Miniformschluss verhindert.
Der Reibbeiwert beträgt damit nicht mehr μ=0,6, sondern weniger. Wieviel weniger weiß keiner der Beteiligten, aber es wird der Wert 0,6 angenommen.
Beschädigte Antirutschmatten
Weitere Situationen, welche die Wirkung der ARM reduzieren zeigen die folgenden Beispiele:
Antirutschmatten, die schon längst ablegereif sind, werden trotzdem verwendet.
Bei Belastung darf sich die ARM nicht mehr als 30% ihrer Dicke verformen. Im Bild wird diese Vorgabe weit überschritten.
Das Ergebnis sind Ausstanzungen wie in diesem Bild. Der Fuß des Ladegestells steht somit ohne erhöhte Reibung auf der Ladefläche. Die Wirkung ist gleich Null.
Ein weiteres Beispiel für die gleiche Situation. Das Problem lässt sich mit unterschiedlichen Maßnahmen lösen:
- Die Füße des Ladegestells oder der Anlage schließen, damit eine größere Fläche entsteht.
- Die Größe der Aufstandsfläche so berechnen, dass sich der Flächendruck auf die ARM reduziert und damit das Durchstanzen verhindert wird.
- Schwerlast-ARM verwenden.
Antirutschmatten aus Gummigranulat
Vorsicht ist auch geboten beim Verwenden ARM die nicht aus Gummigranulat bestehen. Neuwertig haben sie einen sehr hohen Reibbeiwert. Manche Herstellen geben den Wert von μ=0,8 an. Sie sind aber sehr anfällig gegen Schmutz und Staub. Sie sollten daher erst unmittelbar vor dem Absetzen der Ladung gelegt werden.
Nach ein- bzw. mehrmaligem Gebrauch sehen diese ARM zum Teil wie im Bild rechts aus. Die rutschhemmende Beschichtung löst sich und damit ist die Wirkung, bzw. der hohe Reibbeiwert nicht mehr gegeben.
Zusätzliches Niederzurren verhindert Kippen
Wenn ARM verwendet werden, muss die Ladung immer durch Niederzurren zusätzlich gesichert werden. Der Grund dafür sind die senkrechten Beschleunigungen, die beim Fahren über Fahrbahnunebenheiten, Schlaglöcher Bordsteinkanten, Bodenwellen, Teerkanten usw. entstehen. Sie reduzieren die Normalkraft, mit der die Ladung auf die Ladefläche drückt, wodurch der Reibbeiwert und damit auch die Reibkraft reduziert wird.
Ladung mit einer geringen Kippstabilität fängt sofort an zu kippen, wenn ARM verwendet werden. Ohne ARM würde eine solche Ladung erst rutschen und dann kippen. Dieses Kippen wird durch Niederzurren ebenfalls verhindert. Hier ein Beispiel dazu:
Fazit
Bei Kontrollen durch die Behörden spielt der tatsächlich vorhandene, gefühlte oder geschätzte Reibbeiwert eine große Rolle. Bei der Berechnung der Sicherungsmaßnahmen kann es einen erheblichen Unterschied machen, ob mit dem Wert 0,6 oder 0,5 gerechnet wird. Das Ergebnis kann die als ordnungsgemäße bewertete Ladungssicherung sein oder ein Bußgeldbescheid, weil sie mangelhaft vorgenommen wurde.
Alle Beteiligten sollten sich deshalb mit dem Thema beschäftigen und Sorge dafür tragen, dass der Reibbeiwert immer möglichst hoch ist.
Maßnahmen dafür sind u.a.:
- Herstellen der besenreinen Ladefläche
- Kontrolle der Antirutschmatten auf Ablegereife
- Vorgabe eines Ladungsabhängigen Verladeschemas
- Vorgabe der Größe und Anzahl der erforderlichen ARM
- Die Ladung durch Niederzurren zusätzlich sichern
Ihr Sigurd Ehringer
<< Zum vorherigen Beitrag
Folge 38: Wie funktioniert eine Anti-Rutschmatte? – Teil 1: Das Wirkungsprinzip
Zum nächsten Beitrag >>
Folge 40: Wie vermeidet man den Dominoeffekt bei der LKW Beladung?
Sigurd Ehringer
✔ VDI-zertifizierter Ausbilder für Ladungssicherung ✔ Fachbuch-Autor ✔ 8 Jahre Projektmanager ✔ 12 Jahre bei der Bundeswehr (Kompaniechef) ✔ 20 Jahre Vertriebserfahrung ✔ seit 1996 Berater/Ausbilder in der Logistik ✔ 44 Jahre Ausbilder/Trainer in verschiedenen Bereichen —> In einer Reihe von Fachbeiträgen aus der Praxis, zu Themen rund um den Container und LKW, erhalten Sie Profiwissen aus erster Hand. Wie sichert man Ladung korrekt und was sind die Grundlagen der Ladungssicherung? Erarbeitet und vorgestellt werden sie von Sigurd Ehringer, Inhaber von SE-LogCon.