As announced in episode 53, I want to go further into practice, point out mistakes that are often made and present possible solutions.
I am again guided by the three pillars for the fulfillment of duties.
The following personnel measures can be detailed as follows.
– Training – Instruction – Further training |
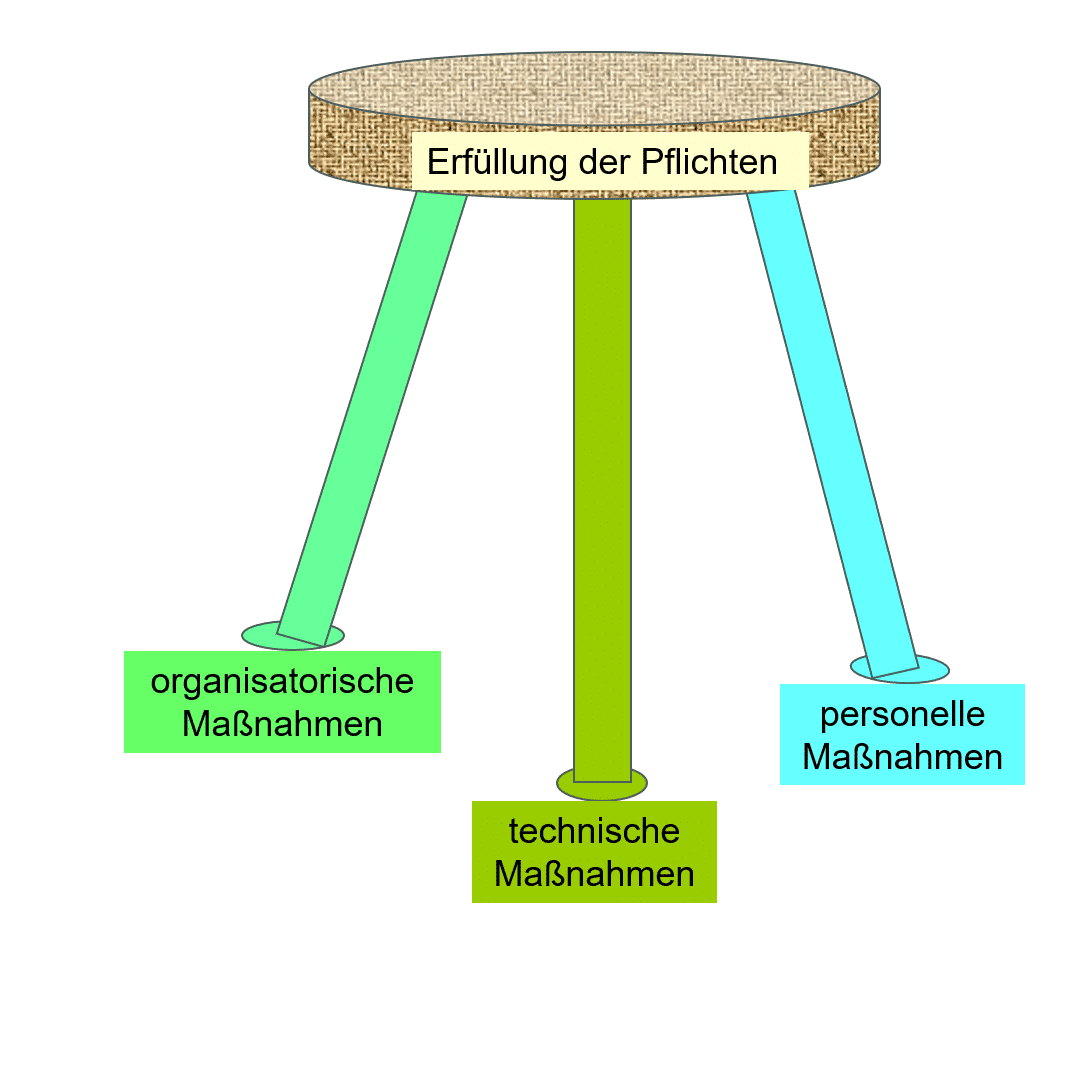
Training and further education of employees
Employee training and development is a cost and time block that is often the first to be targeted and reduced when cost-cutting measures are implemented. This is a very short-term solution and also a dangerous one.
According to the motto “savings will be made no matter what the cost”, little thought is given to the medium and long-term consequences.
A basic distinction must be made between three groups in training and further education:
- Measures that are prescribed by law or regulation and may be subject to time limits, as well as those that
- make sense,
- because they increase efficiency,
- Avoid transport damage
- Making processes and procedures more sustainable and much more.
- are necessary because they are a prerequisite for the deployment and utilization of employees.
Training courses:
It is necessary to prepare employees for their planned deployment. In principle, this applies to all activities. For certain tasks, however, training, education or certificates are essential and must be provided before starting work. In the event of accidents/incidents, this has considerable negative consequences for the employer.
It may also be the case that a considerably greater amount of time and money is required to obtain certificates again if they expire. Companies dealing with dangerous goods should pay particular attention to this.
In the event of an inspection of dangerous goods transports, the lack of certificates and proof of instruction has fatal consequences, including financial ones.
Instructions:
Those who know what they are doing do it better, faster, safer and more reliably. This applies to all activities. It therefore makes sense to check procedures/processes for efficiency and train employees accordingly. To ensure repeatability, procedures/processes should be documented.
Such documentaries are often found as extensive prose works. In times of language barriers, cultural diversity and different mother tongues, this method means that the documentaries are not read, or not read thoroughly. It is merely proof that there is one!
Whether it makes sense and brings the desired success is often not asked. The image/text combination has proven to be a better method. Combine a short, concise text with an image.
Damage >10% of the thickness = ready for discarding
German:
Damage >10% of the width = ready for discarding
Turkish:
Genişliğin %10’undan fazlası hasar = atılmaya hazır
English:
Damage >10% of the width = ready for discard
Someone who cannot read the text accurately will understand that such a belt is unacceptable and therefore unacceptable.
With this basic principle of representation, workflows can also be displayed step by step.
This method ensures reproducible repeatability and thus improves quality and prevents/avoids e.g. transport damage: Transport damage. The simple texts can also be translated into other languages without major problems. This also offers the possibility of involving employees with corresponding native languages. This increases motivation and acceptance.
Using such documents/documentation, instructions/instructions can be carried out with a considerable degree of repeat accuracy. The employer no longer has the risk of whether the instructor remembers all the details and boundary conditions and conveys the necessary content comprehensively.
If checks are carried out on the basis of these descriptions, it is easier to identify deviations and order “instructions for cause”. This makes it much simpler and easier to fulfill the obligation to instruct, as experience has shown that there is no shortage of opportunities.
As each process description must have a corresponding title, proof/documentation can be provided by means of the title and issue date. E.g.: “The employees listed below have taken part in the instruction on discard maturity based on the process description “Discard maturity dated 31.03.2024”“.
Further training:
Mandatory training includes, for example, a forklift license or crane training. Unfortunately, it has been observed time and again that employees are working in this area without any proven training. In my core area of load securing, I repeatedly come across companies that have been stowing goods on trucks and/or in sea containers for years and the employees have not taken part in any training.
VDI 2700 Sheet 5 says in the chapter:
“4.4.2 Training
The employer shall arrange for regular training of persons entrusted with load securing tasks as required, but at least once every three years. The training should cover topics from the following areas:
– Legal responsibility for transportation and load securing
– Physical principles of load securing
– Properties of the load
– Load securing options
– Work instructions for load securing
– Practical implementation of load securing measures using standard operational examples
– Procedure for special load securing cases
The employer shall document the training course with at least the date, participants, content and signature of the participants.”
This makes it clear that training/instruction has a corresponding scope, which presupposes sufficient specialist knowledge on the part of the instructor and also requires the instructor to be qualified to teach. Having extensive specialist knowledge and being able to impart it are two different things. It is in the employer’s own interest to ensure that these conditions are met. Relying on the many years of experience of employees involves risks. “Some people think that what they have done wrong for 20 years is experience.” The person who is to carry out the instructions should be trained by competent institutions/persons and only then deployed.
In this context, the statement in the CTU Code 2014 in chapter 13.1.5 is also interesting:
13.1.5 The management of a facility where CTUs are packed is responsible for ensuring that all persons involved in the packing of cargo into CTUs or in the supervision of this operation are appropriately trained and qualified in accordance with their responsibilities within their organization.
It would be desirable if other regulations also made responsibility as clear as this. To round off the topic, it is also necessary to talk about the documentation of training and instruction. Unfortunately, practical experience shows that employees repeatedly manage to slip through the gaps in the organization and fail to attend events.
This is an organizational problem. A responsible person, regardless of the level, should have an overview/name list of their employees. Sometimes attempts are made to undermine this with the killer argument of “data protection”. This is of course counterproductive.
This list of names must also include an overview showing which employees must have which training, instruction and education and at what intervals. The second advantage is that the names are regularly reproduced correctly. Even if everyone calls the employee “Sepp”, his name would appear in the list as “Josef Müller”.
The list would also solve the problem with the spelling of names where the ten-finger spelling method struggles.
This overview can also be used to plan events throughout the year and it is no longer necessary to squeeze safety briefings into the last three weeks of the year as part of a deadline panic.
The financial expenditure required for the training can also be derived from this and must therefore be planned.
Of course, an Excel list is the simple solution that can be replaced by another tool at any time, as long as it leads to the same goal.
Every entrepreneur or responsible person should check or have checked how things are actually going in their area and take action if there is a need for action. You will be amazed at what you find when you put on the appropriate glasses.
With this in mind, I wish everyone happy work and good luck.
Until the next blog
Yours, Sigurd Ehringer
Previous article >>
Episode 53: Who is responsible in companies – technical measures
Thomas Bauer
✔ Marketing | Web | CI