In most cases, securing the load with form-fit securing methods is the best, simplest and safest solution. In practice, however, it is often unclear which boundary conditions must be met for this to actually work.
Boundary conditions from the standards
EN 12642 has been around since 2007 with the unwieldy title: “Securing loads on road vehicles – Bodies on commercial vehicles – Minimum requirements; German version EN 12642:2016“.
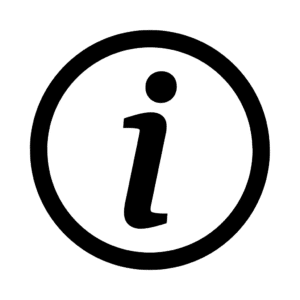
Most use the common short title “EN-12642 Code XL”. During the development of the standards, the superstructures were divided into two groups. The so-called standard superstructure code L with maximum strengths of the superstructure and the reinforced superstructure code XL with minimum strengths.
The specifications relate to the front wall, the side walls and the rear portal. Testing of the floor load is not included because this is already included in EN-283. The standard gives body manufacturers a lot of freedom as long as the tested strengths are within the specifications.
The following overview is an excerpt from the standard with the current specifications. The letter “P” stands for the technical payload of the vehicle or body. For standard semi-trailers, this is usually 27,000 kg.
The strength of the end wall must be tested over the entire width and up to three quarters of the height. This area must be taken into account to ensure positive locking. Pay particular attention to the loading width.
For the shipper, there are also three important control aspects, namely
- the labeling obligation specified in the standard
- Proof of each structure with a certificate
- the manufacturer’s requirement that the superstructures must be checked once a year
This type of spacer acts on the front wall like a can opener. In the event of emergency braking, the bulkhead would simply be pushed through. The shipper must therefore ensure that the end wall is loaded at least over its entire width.
Boundary conditions of the manufacturers
So much for the boundary conditions specified by the standard. The manufacturers have also formulated boundary conditions so that the superstructures can absorb the forces. These are described in the certificate in relation to the respective structure.
In practice, it has been shown that these boundary conditions are essentially the same for all manufacturers.
They are:
- Sliding friction coefficient of at least μD = 0.30
- Form-fit loading in the direction of travel
- Load width at least 240 cm
- Max. Permissible distance load/back wall 15 cm
In most cases, special specifications are made for special loads, such as beverages, which both the vehicle owner and the shipper must adhere to.
What does the whole thing look like in practice? The truck arrives in the loading zone, the driver pushes open the left-hand tarpaulin, the forklift driver places the load on the loading area, the driver closes the tarpaulin again and drives off. This is roughly how most shipments work.
Necessary measures
1. the shipper should check whether the driver has the Code XL certificate with him and read it to determine which special features must be observed
.
An eye check is then required to ensure that the build-up strength is not impaired by damage. Finally, the proof of the annual inspection must be checked.
Vehicles with damage as shown in the picture should not be loaded under any circumstances.
2. such a marking would not replace the certificate, but would suffice as Code XL proof for the time being. According to the new labeling regulations, the load capacity of the end wall must even be indicated at different heights.
3 Finally, the proof of the annual inspection must be checked. They could look like this or similar, but the paper form would also be fine.
4 The manufacturer specifies that the coefficient of sliding friction should be at least μD=0.30. This condition can be achieved if the driver sweeps the loading area properly with a broom.
Broom clean, that’s the magic word. Many screws can be turned in load securing, but a lot can be done with the “friction screw”. The shipper must therefore demonstrably ensure that the loading area has been swept before loading.
Form-fit loading in the direction of travel
Form-fit loading in the direction of travel means that the load units are lined up without gaps, starting at the front wall. It is important that the forces from the individual load units are transferred to the end wall throughout.
Unstable, over- or under-built loading units do not do this. Example:
Such a load will move into any free gap. The load unit securing is completely inadequate.
Superstructure pallets transfer the forces via the product to the end wall or other load units. Damage is inevitable.
Whether the body strengths can actually secure the load via positive locking depends crucially on the type of load units and how they are secured. It is grossly negligent to talk about positive locking with such a loading unit, as the bulkhead will inevitably be damaged.
Form-fit loading to the side
Form-fit loading to the side means that the load width must be at least 2.40 m according to the manufacturer’s specifications. The internal width of today’s standard bodies is between 2.40 m and 2.50 m, depending on the design and body type. The specification of 2.40 m can be traced back to the Euro dimension.
This means that two Euro pallets can be placed crosswise or three lengthwise in a row. Of course, the same requirements are again placed on the load units, which must be stable in shape and tilt so that the centrifugal forces are transmitted without gaps when cornering or swerving.
Positive rear loading
The sum of the permissible gaps results from the maximum internal width of the body, minus 2.40 m. A common dimension is 8 cm as the total gap.
Form-fit loading to the rear means that the distance to the rear portal must not exceed 15 cm. If the gap is greater, it must either be filled in or the load must be secured to the rear. There are several solutions to fill the gap. The most common solution is to use Euro pallets.
If the pallets are stowed upright, care must be taken to ensure that they do not fall out when the rear door is opened.
It is therefore better to position the pallets in front of the last loading row.
Summary of the specifications
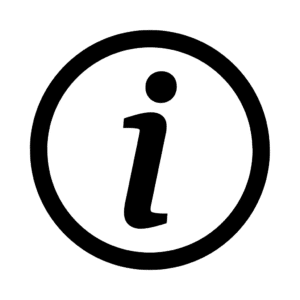
This extract can be found in most certificates:
“If all the requirements of no. 2 to no. 5 are fulfilled, load securing is guaranteed by the stability of the vehicle body. Additional securing measures such as tie-down lashing or direct lashing are no longer necessary. Additional securing measures in accordance with VDI 2700 are required for deviating load cases.”
This means that if the specifications I have described above are not met, the manufacturer does not guarantee that the body can absorb the securing forces. The responsible shipper is therefore required to demonstrably ensure that the necessary measures/checks are carried out.
If not, he must apply the methods according to “VDI-2700 “Load securing on road vehicles” (the recognized rules of technology) in accordance with §22 StVO “Load”. If the worst comes to the worst, he must also provide evidence of how the load was secured at the time the truck left the shipper’s area of responsibility.
Unfortunately, practice shows that people often work with a lot of luck.
Yours, Sigurd Ehringer
<< Previous article
Episode 22: Floor loads on trucks
Next article >>
Episode 24: Avoiding recourse claims
Sigurd Ehringer
✔ VDI-zertifizierter Ausbilder für Ladungssicherung ✔ Fachbuch-Autor ✔ 8 Jahre Projektmanager ✔ 12 Jahre bei der Bundeswehr (Kompaniechef) ✔ 20 Jahre Vertriebserfahrung ✔ seit 1996 Berater/Ausbilder in der Logistik ✔ 44 Jahre Ausbilder/Trainer in verschiedenen Bereichen —> In einer Reihe von Fachbeiträgen aus der Praxis, zu Themen rund um den Container und LKW, erhalten Sie Profiwissen aus erster Hand. Wie sichert man Ladung korrekt und was sind die Grundlagen der Ladungssicherung? Erarbeitet und vorgestellt werden sie von Sigurd Ehringer, Inhaber von SE-LogCon.