As announced in episode 51, I want to go even deeper into the practice and point out mistakes that are often made.
I am again guided by the three pillars for the fulfillment of duties.
The following organizational measures can be detailed as follows.
1. appointment of authorized persons 2. Organization of processes 3. Creating instructions 4. Drawing up checklists 5. Monitoring the execution 6. Definition of 100% controls 7. Definition of random checks |
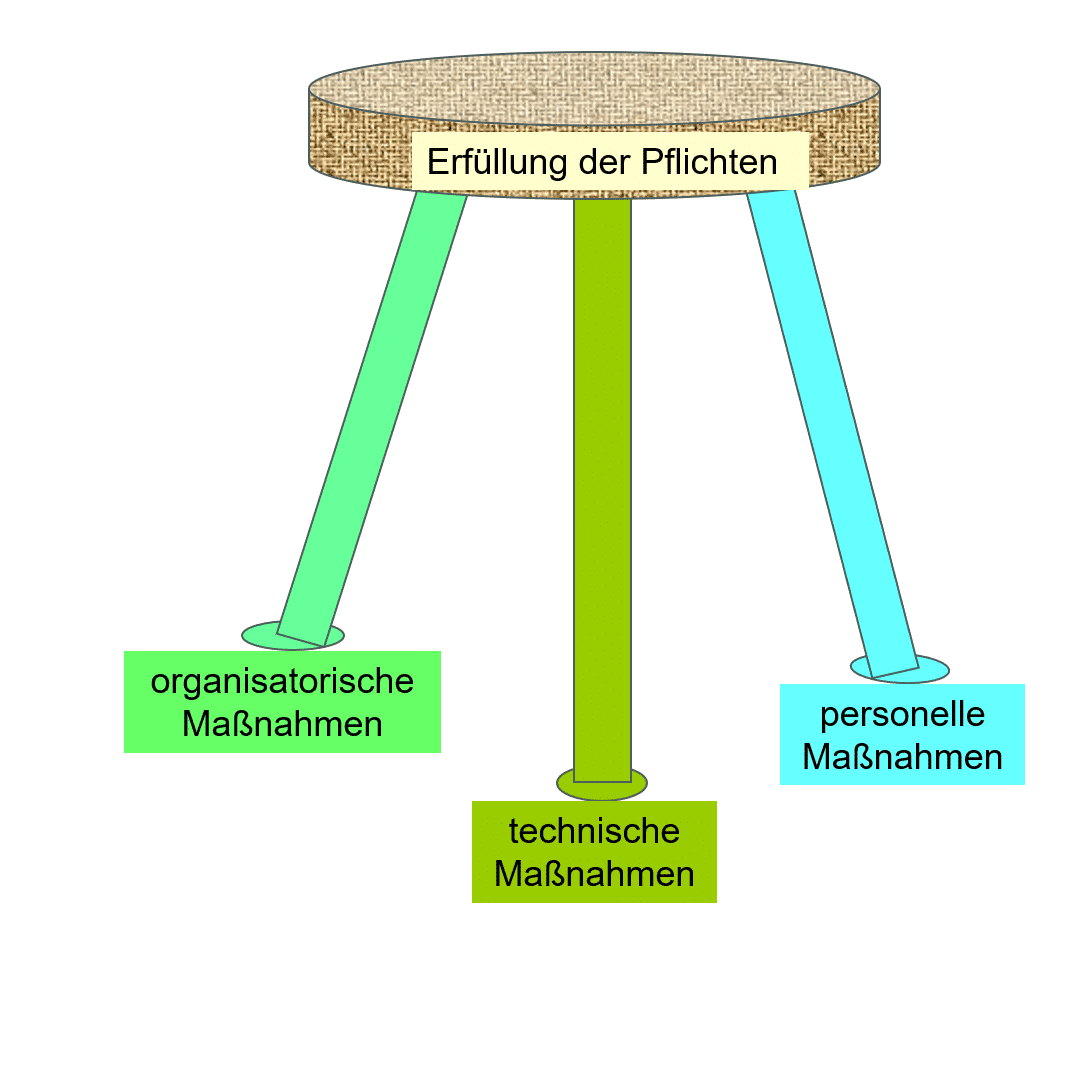
Error 1
No appointment of an authorized person
One of the most common mistakes that are made is that appointed persons are not appointed in the first place. This means that there is no decisive basis for being able to hold them accountable for anything. An employment contract can of course also replace this appointment, provided that it clearly states what the person concerned is to be held responsible for in the event of an incident.
The second mistake is the fact that the person concerned is expected to take responsibility, but is denied the authority to make decisions and changes. This contradicts §9(2) OWiG “Acting on behalf of another”, which states: “expressly instructed to carry out tasks on their own responsibility that are incumbent on the owner of the company“.
If this is not the case, the responsibility automatically falls back to the managing director. The managing director must also provide evidence of the way in which he/she has controlled/supervised the person concerned. If there is no planned process for this either, the managing director becomes jointly responsible. It is up to the managing director to decide whether the appointed person submits regular reports or whether there is a JourFix with a meeting/reporting/presentation or another type of supervision. No verifiable process is the decisive error.
Error 2
No organization of processes in the company
Processes must be organized in such a way that the likelihood of administrative offences, misconduct or legal violations is low. If incidents do occur, they must be identified at an early stage in order to minimize the impact.
The following situation serves as an example. A company works in three shifts and loading takes place during each shift. However, the appointed “head of loading operations” is only on site during regular working hours. There is no decision-maker or supervisor for the individual shifts.
If something goes wrong, the responsibility remains with the head of loading and if he does not order properly, it falls back to the managing director. Care must therefore be taken to ensure that a decision-maker is available at all times.
The simplest solution is for the head of loading to have three deputies, one on each shift.
Error 3
No action definition for employees
The lower levels of employees, and that is most of them, work according to instructions. These instructions contain descriptions of how the employees are to carry out and fulfill their tasks.
The main mistake is that there are no instructions of any kind. If there are no instructions, then controls are not possible or are very difficult. Because what is to be checked? For example, the instruction “sufficient load securing equipment must be provided” is not really appropriate. What is the employee concerned supposed to ensure? He is dependent on what a truck has with it. Whether it is the right one and in sufficient quantity is something he cannot influence.
There must be a requirement for the transporter in advance in which it is clearly defined which securing equipment must be provided and in what quantity. Depending on the load, this can or must also be extended to the type of vehicle, its payload, its equipment (for the transportation of hazardous goods), etc.
The responsible loading employee can check these specifications on the basis of the specification. Whether he only needs 6 of the ten required tension belts, for example, then depends on the specific loading situation. If all ten tension belts are required, they must not be ready to be discarded. If this is the case, the instructions must also include a standard solution. Only if the loading employee has not complied with the instructions can recourse be taken against him in the event of a violation of §22 StVO.
No instruction, no responsibility, no recourse.
Error 4
No formulated instructions and checklists
Checklists are a good way of instructing employees to work through certain processes in a set order. You can think of it like a recipe in which certain ingredients and quantities, as well as the order of preparation, are specified.
A common argument is “I don’t have enough time”. If the recipe states to leave the dough in the oven at 120 degrees for 40 minutes, then it makes no sense to stop after half an hour because the time available is too short. This connection is intended to symbolize planning errors in the organization of processes.
If possible, the checklist should contain measurable values or information, or it should be possible to answer yes or no. If the checklist is to be used for monitoring purposes, it must contain work instructions.
The individual measurable and verifiable steps of a work instruction are checked and documented using the checklist. Checklists for each transport have proven to be particularly useful when dealing with dangerous goods. The detailed regulations from dangerous goods legislation can be easily implemented in the form of checklists.
Error 5
No regular implementation checks
A responsible person is obliged to fulfill their duty of supervision in the form of checks. The legislator does not make any detailed regulations on the “how”.
The person responsible should not rely exclusively on reports from the bottom up. Every report is filtered and colored on its way through the various levels, especially if it contains unpleasant information.
Every manager should regularly take the time to look around their area, talk to employees and get an unfiltered impression.
If such inspections also take place unannounced and by chance, his impression is more likely to correspond to reality than he can get from written reports.
Error 6
No 100% checks
The 100% check is proof from the relevant employees that every process has been carried out and work instructions have been implemented correctly.
Example: The signatures of the driver and loader on the delivery documents confirm the proper and complete handover of the goods. This signature can also serve as confirmation by the loader that he has checked the truck in accordance with the specifications and secured the load in accordance with instruction “4711”.
The cost of this confirmation is low, but of great benefit.
Error 7
No random checks
Random checks have a different purpose. If 100% checks are not possible due to large quantities, random checks can be carried out according to defined quantities or batches. However, another important purpose is to verify,
- whether the 100% controls reflect reality,
- whether the processes still meet the requirements,
- whether workflows/processes need to be adapted, changed or can be omitted altogether or need to be set up from scratch.
They are therefore an important management tool at all levels. These checks should be carried out by the line manager themselves or by an employee who is not directly involved.
For example, the checks on the first shift could be carried out by an employee from the second shift if the supervisor instructs them to do so. The inspector does not need to understand the processes down to the last screw, but he does need to understand the essentials so that the inspection produces the correct result.
Much more could be said about the “Organizational measures” pillar using further examples. What matters to me is to initiate a thought process in order to take the tips and thoughts back to your own company and see how things are going.
Happy working until the next blog, in which I will discuss the extensive second pillar.
Yours, Sigurd Ehringer
<< To the previous post
Episode 51: Who is responsible in companies?
To the next post >>
Thomas Bauer
✔ Marketing | Web | CI