Load securing on/in trucks is usually form-fit or force-fit. I described what the form-fit method is all about and what you need to bear in mind in episode 23.
In this episode, the securing device “tension belt” will be described in more detail, especially from the perspective of “discard maturity”.
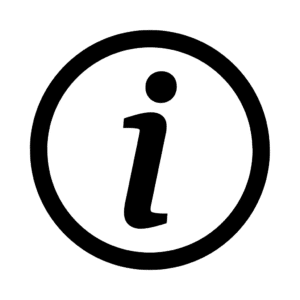
The regulation for manufacturing and testing lashing straps is EN-12195-2 “Securing loads on road vehicles” Safety Part 2 “Lashing straps made of man-made fibers” 2001-02.
The standard only refers to manually operated clamping elements with a maximum SHF of 500N=50daN. This is the normal force that must be applied to achieve the preload force (STF) specified by the manufacturer.
This standard is essentially a test specification, but it also describes the conditions of use and labeling.
Components of a lashing
Discard criteria for lashing straps
Another set of rules is VDI-2700 Sheet 3.1 “Instructions for use of lashing equipment” 03-2023. The definition of damage is new. The directive specifies a measurable value here.
Damage must not exceed 10% of the cross-section. This applies to both the width and the thickness of the material. In practice, damage is often not sufficiently taken into account in relation to the material thickness.
With a webbing material thickness of approx. 3 mm, damage of 10% = 0.3 mm is quickly reached.
Both belts are ready to be discarded.
Excessive wear is also a discard criterion. This is not easy to assess. The picture shows a belt with the kind of damage that occurs when the same load is always secured. Edge protection angles or hose edge protection would prevent such damage.
This belt is ready for discarding.
Such damage occurs when the belt is hooked in and the insertion slats then rest directly on the belt. This will inevitably damage it.
This belt is ready for discarding.
Belts that are damaged at the seams or have been improperly repaired or manufactured, as shown in the pictures, are not permitted and must not be used.
This belt is ready for discarding.
Excessive rust due to improper storage or storage on the vehicle.
This belt is ready for discarding.
This damage to the webbing indicates improper handling.
This belt is ready for discarding.
Such damage to the ratchet occurs if the operator uses a bar, nailing iron or metal pipe as an extension of the clamping lever. The maximum manual force of 50 daN was far exceeded.
Extensions are generally not permitted unless they are specially designed for this purpose.
This belt is ready for discarding.
Damage to a belt due to overstretching caused by an impermissible lever extension. Only 35 mm of the original belt width of 50 mm remains.
This belt is ready for discarding.
The buckling test
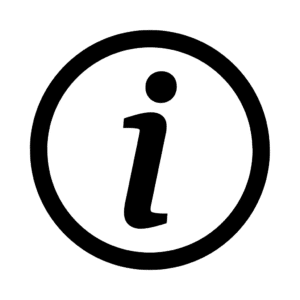
The buckling test has proven its worth in making it easier to decide whether the material is ready for discarding, especially when it comes to damage in relation to the material thickness.
The strap is placed over the damaged area of the finger or bent.
It is easy to see whether the 10% limit has been exceeded or not.
Example: The damaged belt is hanging on the insertion bar.
The buckling test shows that the belt is definitely ripped because the damage is more than 10% of the material thickness.
Conclusion
It is important that the belts on a vehicle are checked regularly. This is the responsibility of the driver as the user, but also of the vehicle owner. The driver is obliged to check the belt for discarding before each use.
The vehicle owner must provide written proof that the seat belts have been checked at least once a year by an expert.
However, the loader (managing director or appointed representative) must also ensure that no belts that are ripe for discarding are used in the specific loading situation. In the event of an incident that would result in an administrative offense, but in any case with criminal consequences (e.g. negligent bodily injury), the shipper would also be responsible. The best way to do this is with a checklist for an incoming goods inspection, which includes the point of the belt check and forms part of a work instruction.
Yours, Sigurd Ehringer
<< Previous article
Episode 28: Prestressing force (STF) and lashing capacity (LC)
Next article >>
Episode 30: Damage to the truck – when should you refuse a load?
Sigurd Ehringer
✔ VDI-zertifizierter Ausbilder für Ladungssicherung ✔ Fachbuch-Autor ✔ 8 Jahre Projektmanager ✔ 12 Jahre bei der Bundeswehr (Kompaniechef) ✔ 20 Jahre Vertriebserfahrung ✔ seit 1996 Berater/Ausbilder in der Logistik ✔ 44 Jahre Ausbilder/Trainer in verschiedenen Bereichen —> In einer Reihe von Fachbeiträgen aus der Praxis, zu Themen rund um den Container und LKW, erhalten Sie Profiwissen aus erster Hand. Wie sichert man Ladung korrekt und was sind die Grundlagen der Ladungssicherung? Erarbeitet und vorgestellt werden sie von Sigurd Ehringer, Inhaber von SE-LogCon.