There are more load securing methods than you might think.
However, the tie-down lashing method is usually used, even though it is not very efficient.
The book lashing
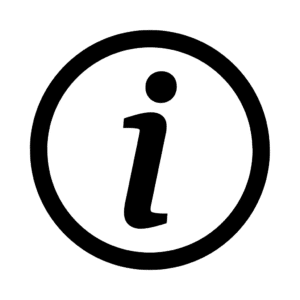
Bay lashing or strapping lashing (EN-12195-1) is a securing method that can be used simply, safely and efficiently for certain loads.
It is important to know that the securing force only works in one direction at a time.
Suitable loads are machines, systems, equipment, etc. where the securing devices can be passed through attachment points, eyelets, openings, recesses, etc.
Care must be taken to ensure that no sharp edges can impede the distribution of clamping force or damage the securing material.
When securing long loads such as masts, prefabricated concrete parts, pipes (also bundled) etc., securing can be carried out as follows.
Coming from one side of the loading area, the securing equipment (blue) is looped around the load or suitable positions on the load and returned to the same side. The belt guide (orange) is used in the same way on the opposite side.
The load is held in position after the securing devices have been tightened by hand.
The lashing angle α between the two ends on each side must be taken into account.
The factor 0.75 must be used for ƒμ in order to take dynamic situations into account for friction.
This means that the frictional force is reduced by the factor and the required securing force is therefore higher.
Graphical representation
Two lashings must always be attached at right angles to the direction of travel, one on the left and one on the right, to prevent the load from twisting.
It is advantageous if a securing device is attached to two different lashing points on the cargo bed, as this allows the LC to be used twice.
The graphic shows an excerpt from EN 12195-1 with a calculation example.
Alternative method
A variant of this lashing method is similar to direct lashing, but the connection to the load (10,000 kg) is made using belt loops.
The straps are each attached to two different points on the loading surface, doubling the LC.
This method is simple, quick to install and provides a high securing force.
Roughly calculated, a belt provides a securing force of 4,000 daN. In the direction of travel therefore 8,000 daN. Friction is not taken into account here.
It almost compensates for the reduction in securing force due to the lashing angle.
When hanging the straps in the perforated strip, the spacing specifications of the body manufacturer must be observed if necessary.
In the example on the right: max. 8,000 daN per meter of perforated strip.
The situation in the loading example above would therefore be correct.
The securing force
In the fictitious example, the calculated securing force, taking into account the lashing angles α and β, must be 2,445 daN per lashing.
In the example, 4,000 daN is calculated per strap, i.e. almost 1,500 daN more than required.
If the load were placed on anti-slip mats, which is always sensible, and a coefficient of friction of μ=0.6 were taken into account, the safety cushion would be even greater.
Conclusion
The situations described above show that, with thought and practical knowledge, load securing can be made simple and safe.
Unfortunately, practical knowledge in both the shipper and driver sectors is not yet as developed as it would be desirable.
One of the things I would like to do with my contributions is to encourage people to pay more attention to this issue in the interests of general road safety and to promote internal solutions.
Yours, Sigurd Ehringer
<< Previous article
Episode 34: Head lashing & cross lashing – application and possible uses
Sigurd Ehringer
✔ VDI-zertifizierter Ausbilder für Ladungssicherung ✔ Fachbuch-Autor ✔ 8 Jahre Projektmanager ✔ 12 Jahre bei der Bundeswehr (Kompaniechef) ✔ 20 Jahre Vertriebserfahrung ✔ seit 1996 Berater/Ausbilder in der Logistik ✔ 44 Jahre Ausbilder/Trainer in verschiedenen Bereichen —> In einer Reihe von Fachbeiträgen aus der Praxis, zu Themen rund um den Container und LKW, erhalten Sie Profiwissen aus erster Hand. Wie sichert man Ladung korrekt und was sind die Grundlagen der Ladungssicherung? Erarbeitet und vorgestellt werden sie von Sigurd Ehringer, Inhaber von SE-LogCon.