Load distribution in containers is always a topic of discussion. In contrast to the old “CTU Packing Guidelines”, the CTU Code 2015 is not a recommendation, but a binding set of rules containing specifications that must be complied with and can also be monitored.
The gap sum can be used as an example here. The inspection officer of the shipping company or port authority opens the container, measures the distance from the rear door to the load and complains about the load securing if the distance is more than 15 cm and he cannot recognize adequate securing. He immobilizes the container or has it repaired for a fee.
If the distance to the container door is more than 60 cm, it is likely that the container has been loaded incorrectly and the load distribution specifications have not been complied with. The inspector does not even have to do the math, it is enough to measure the distance because the detailed inspection will probably prove him right.
Load distribution is important because although spreaders are used in large, modern ports to compensate for a shifted center of gravity on the harness, this is not necessarily the case in subordinate ports. The tolerance of the cell guides, the guide rails on which the containers slide down into the hull over 9-11 container layers, is 4-5 cm.
This spreader can compensate for a deviating center of gravity.
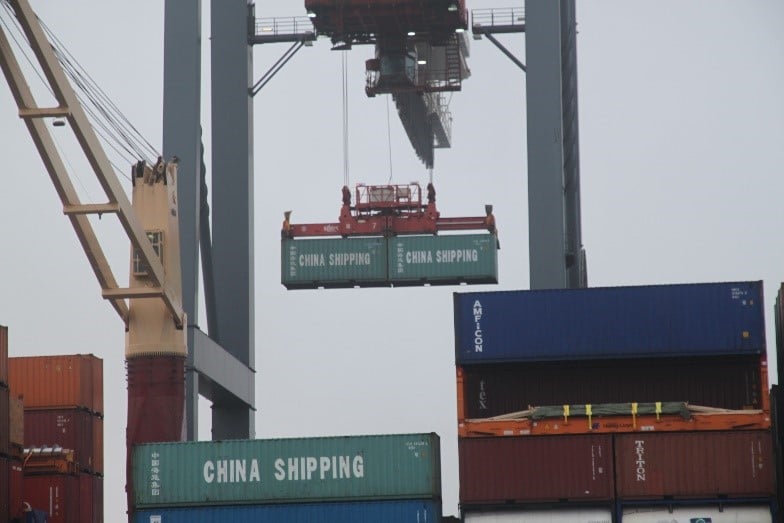
This spreader cannot do this because the lines of force converge at one point on the hook.
What about load distribution?
The CTU Code makes clear specifications regarding the focus in Appendix 7, section 3.1.4:
“In general, the off-center center of gravity of the load should not be more than ±5%. As a rule of thumb, 60% of the total mass of the load can be assumed to be 50% of the length of the freight container. Under special circumstances, a deviation of up to ±10% could be accepted, as modern loading gear for handling ISO containers is capable of compensating for such deviations. The exact position of the center of gravity in the longitudinal direction of the load can be calculated (see Appendix 4) “.
The situation is easier to visualize as a graphic.
In section 4.2.2 on page 18, the CTU Code assigns the shipper the obligation to inform the charterer (shipping company; carrier) of any deviations in the center of gravity.
The problem now facing the responsible loader is the question of how to ensure this condition. The solution is called a stowage plan! Unfortunately, this is rarely created, which of course leads to problems. The loader usually starts with the nice, convenient load at the front, hoping that he will come up with a solution for the problem load during the stowage. As this is often not the case, it is in the door area and is the first thing the inspector sees.
This is the formula from the CTU code that can be used to solve the problem of load distribution. What expectations do the CTU code writers have? Some people will be put off by the visual impression of the formula.
However, the formula is easy to explain. The force exerted by each individual load unit must be calculated using the lever principle.
This is a laborious task and requires the center of gravity and weight of the load unit to be known.
With normally packed Euro pallets, it can generally be assumed that it is in the middle. This means 60 cm or 40 cm from the edge of the pallet, depending on how they are stowed.
In the case of machines and systems, the design department must provide specific details.
This diagram from the CTU Code Appendix 4 on page 133 makes it easier to understand and shows how to measure.
The calculation example from the CTU code can also be used as a template for a calculation table. The sum of all individual calculations is divided by the total weight of the load. This gives the distance between the total center of gravity and the end wall. This distance must then be in the 5% or 10% range of the container.
A classic block of five Euro pallets, which all weigh the same, can be calculated in a simplified way.
5 x 800kg x 1.20m = 4,800kgm
The calculation for the second block of five would be as follows:
5 x 800kg x 3.60m = 14,400kgm
The calculation of the center of gravity then results from:
4,800kgm + 14,400kgm = 2.4m
_________________________________
8,000kg
This position can also be derived purely visually.
If the weight of the pallets differs significantly, each load unit must actually be calculated separately.
For this fictitious example, the calculation would be as follows:
700kg x 0.40m = 280kgm
800kg x 1.20m = 960kgm
900kg x 2.00m = 1,800kgm
1,000kg x 0.60m = 600kgm
1,100kg x 1.60m = 1,760kgm
_____________________________
4,500kg 5,400kgm
5,400kgm / 4,500kg = 1.20m
The total center of gravity of the block of five is 1.20 m from the end wall, even if the load units have different weights. If the load carriers have different dimensions, this is of course not necessarily correct.
The examples shown make it clear that calculating the overall center of gravity is not rocket science. Creating a stowage plan from this, on the other hand, is more difficult.
In companies where this situation occurs regularly, it is worthwhile, with a little diligence, to set up the invoice table in such a way that it can also serve as a stowage plan.
This makes it easier to juggle back and forth. The graphic shows an example of what such a table could look like.
The CTU Code sets out more precise requirements in Annex 7, paragraph 3.1.4. As a rule, the deviation of the center of gravity should be 5% from the center of the container. For a 40-foot container this would be +/-30cm off the longitudinal center and for a 20-foot container +/- 15cm.
If the center of gravity is outside the 10% specification, you can still check whether the 60/40 distribution is successful. This means that 60% of the load weight is in one half of the container and 40% in the other. When applying this 60/40 rule, however, care should be taken to ensure that the 60% is not on the front wall so that the drive axle load of the tractor unit is not exceeded. This can be very expensive in various countries.
All three variants are permissible, whereby the 5% rule should generally be aimed for. If none of the three requirements is successful, the shipper (shipping company/forwarding agent) must always be consulted. This may be the case for machinery and equipment in particular.
Investigations of incidents involving container ships, such as lost containers at sea, repeatedly show that incorrect cargo securing or load distribution in the container can be one of the causes that lead to much greater damage, as in the domino effect. A lost container floating close to the surface is also a considerable danger for general shipping, especially for cruising sailors.
I hope that I have been able to encourage those involved/affected to deal with the situation and develop a company-specific solution. It’s worth the effort, because it costs a lot more time and money to restructure and improve.
Yours, Sigurd Ehringer
Sigurd Ehringer
✔ VDI-zertifizierter Ausbilder für Ladungssicherung ✔ Fachbuch-Autor ✔ 8 Jahre Projektmanager ✔ 12 Jahre bei der Bundeswehr (Kompaniechef) ✔ 20 Jahre Vertriebserfahrung ✔ seit 1996 Berater/Ausbilder in der Logistik ✔ 44 Jahre Ausbilder/Trainer in verschiedenen Bereichen —> In einer Reihe von Fachbeiträgen aus der Praxis, zu Themen rund um den Container und LKW, erhalten Sie Profiwissen aus erster Hand. Wie sichert man Ladung korrekt und was sind die Grundlagen der Ladungssicherung? Erarbeitet und vorgestellt werden sie von Sigurd Ehringer, Inhaber von SE-LogCon.